
Research on the Technological Development of Resilient River Levees against Overtopping
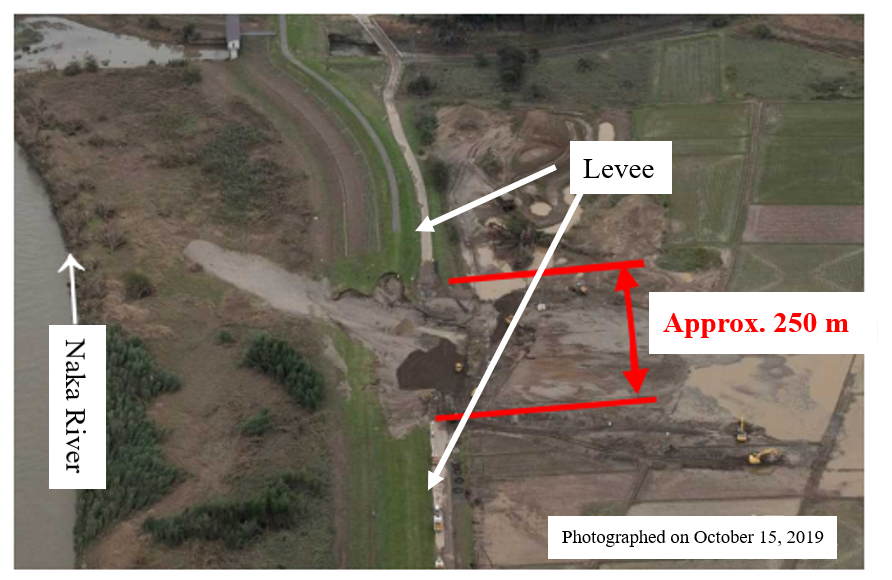
Photo 1 Levee breach on the 28.6 k
(i.e. 28.6 km from the mouth of river)
right bank of the Naka River, Naka River system
(Source: 1) with additional information)
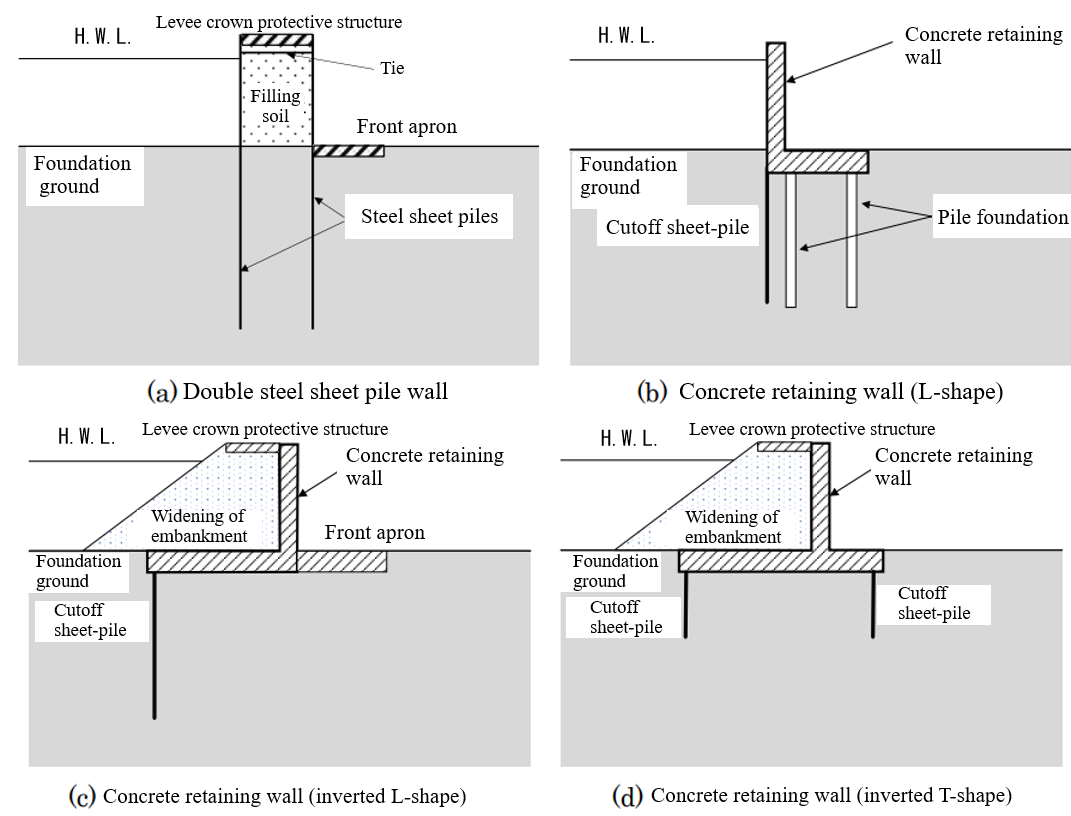
Figure 1 Typical self-standing structures
(source: 2), with additional information)
In 2019, Typhoon No. 19 (Hagibis) caused breaching of 142 levees across Japan. In 86% of these cases, overtopping was presumed to be the primary cause of the breach. Photo 1 shows the Naka River levee, which was breached due to overtopping by the typhoon. Here, overtopping refers to the phenomenon in which the water level of a river exceeds the height of the levees, resulting in river water overflowing the levees. In response to the damage caused by Typhoon No. 19 in 2019, MLIT has been promoting the technological development of resilient river levees against overtopping.
Self-standing levees (including self-standing special levees) are river levee structures that are resistant to overtopping.In case of the self-standing type, it is considered that steel sheet piles are driven into the levee (Figure 1(a)) or that a concrete retaining wall is built in the levee (Figure 1(b), (c), (d)), as shown in Figure 1. The Soil Mechanics and Dynamics Research Team, together with the River Division, River Department, National Institute for Land and Infrastructure Management, MLIT, compiled a guideline for the Technological Development of Resilient River Levees (Self-standing Type) (hereinafter referred to as the “Reference”) (Figure 2) to serve as a reference for the future technological development of resistant river levees (self-standing type), and released it to the public in December 2022.
The team has also been conducting hydraulic model experiments since FY 2022 to investigate the mechanism whereby a self-standing structure is breached by overtopping. In FY 2022, we conducted small-scale hydraulic model experiments of a double steel sheet pile wall structure of the self-standing type. A levee model with a height of 100 mm was constructed and its fracture behavior due to overtopping was investigated (Photo 2). We plan to continue examining the mechanism of fracture caused by overtopping in more detail.
References
1) Technical Review Meeting on River Levees Based on the Damage Caused by Typhoon No. 19 in 2019: Material 2-2 Factors Causing Breaches in Government-Managed Rivers (Study by the Levee Investigation Committee), p.9.
2) River Division, River Department, National Institute for Land and Infrastructure Management, MLIT; Soil Mechanics and Dynamics Research Team, Geology and Geotechnical Engineering Research Group, PWRI: Reference for the Technological Development of Resilient River Levees (Self-standing Type), p.8.
![]() |
![]() |
(Contact : Soil Mechanics and Dynamics Research Team)
Use of Technology for Creating 3D Flood Hazard Maps
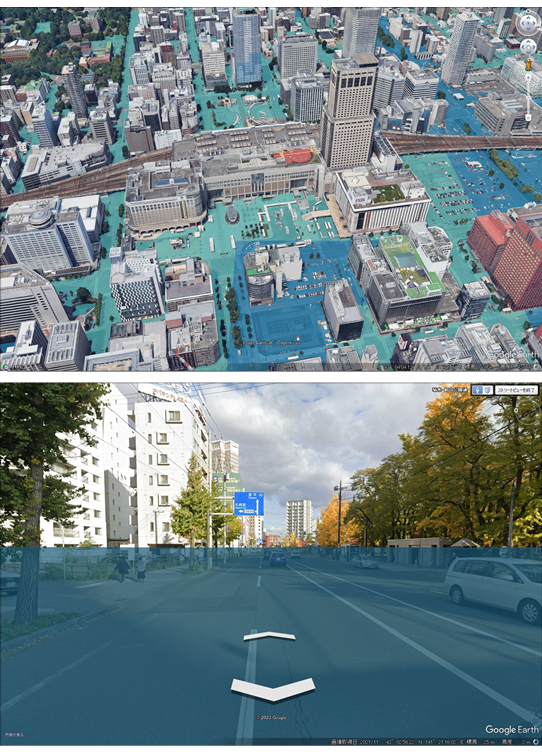
depicted on Google Earth.
Bottom: Google Street View around Nakajima Park
in Sapporo City, showing the estimated flood.)
Every year, some parts of Japan see flooding. Flood hazard maps provide useful information for residents who evacuate. However, not everyone correctly interprets these maps. The River Engineering Research Team is proposing the use of Google Earth and Google Street View to create 3D hazard maps that are easier to understand and use (Figure-1) and is releasing software and a manual for creating these maps free of charge (Figure-2), while also conducting promotional activities. These maps are unique in providing an intuitive understanding of the estimated flood level by showing where the flooding reaches on surrounding buildings.
In addition to giving lectures on this technology at the PWRI New Technology Showcase hosted by the Public Works Research Institute in various locations throughout Japan each year and at disaster prevention-related exhibitions held by other organizations, we have introduced this mapping technology at numerous various disaster-prevention events, including Comprehensive Flood-Fighting Exercises in Hokkaido, and in this web magazine’s March 2022 issue.
・Research results|PWRI (Public Works Research Institute) Web Magazine
The issues that we have learned about through these promotional activities were reported in the February 2023 issue of the Monthly Report of the Civil Engineering Research Institute for Cold Region.
・Overview of 3D Flood Hazard Maps - Benefits and Application Examples
・Tips When Using 3D Flood Hazard Maps
・Mechanism of Rendering 3D Flood Hazard Maps
The following issues remain for these maps.
・Google Earth shows streetscapes, including buildings, in 3D for major cities and their environs, but for most other areas, 2D views are still used. Therefore, it is not possible to show where flood levels reach on surrounding buildings in many regions.
・This technology draws the water surface in the 3D graphic representing the flooding depth on Google Earth, so when it is viewed in Street View, if the flooding depth is great, it appears as if there is a wall in the sky when one looks up, with no water below it. To interpret the image, you need to know how it is displayed (Figure-3).
Unless you know how the image is displayed, the 3D flood hazard maps look strange. If you look at the maps after receiving an explanation, however, you will not be so bothered by the appearance of the map. Thus, for example, the maps could be used in disaster education after the precautions to be taken when reading the maps are explained.
We hope that the use of 3D flood hazard maps along with conventional hazard maps will deepen understanding of flood risks and will lead to evacuation in the event of flooding.
![]() screen for creating 3D flood hazard maps |
![]() displayed on Street View |
(Contact : River Engineering Research Team, CERI)
Development of Technology for Melting Snow from a Distance Using Infrared Lasers
In snowy, cold regions, falling or blowing snow may accrete to road signs (hereinafter referred to as “road infrastructure”). Ice and snow on road infrastructure can enlarge and fall, which can damage road vehicles and other traffic. To prevent this, road administrators regularly remove snow from road infrastructure(Figure-1), but the costs and labor required for such removal are burdens on road maintenance and management. Effective technologies for snow and ice removal are particularly needed in areas where snow cannot be removed without the use of lift vehicles or the like. Therefore, the Civil Engineering Research Institute for Cold Region (CERI) has developed a technology for melting accreted snow and ice using lasers, which can propagate over long distances.
Lasers can have various light sources. To identify the optimal wavelength for melting snow, we decided to study light and ice by going back to the basics. For example, it feels warm to stand in front of a far-infrared radiation lamp. This is because the moisture in human skin absorbs far-infrared light and oscillates, which generates heat. Identifying the specific wavelengths of light that are well absorbed by snow and ice will tell us the optimal laser light source for snow and ice melting.
Based on measurements of the ice-melting rate for lasers of three wavelengths, coefficients were obtained for the ice-melting rate at wavelengths from 1μm to 100μm (μm = 10-6m) (Figure-2). A CO2 laser with a wavelength of 10.6 μm and an Er:ZBLAN fiber laser with a wavelength of 2.85 μm were found to be the most suitable light sources.
Since CO2 lasers that can achieve high power output have been commercially available for a long time, this study utilized a CO2 laser. Snow-melting tests were conducted outdoors (Figure-3).
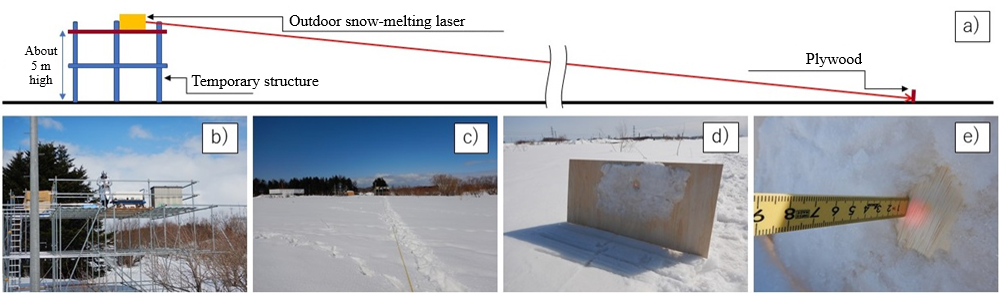
- The CO2 laser used in the test has a light source with a wavelength of 10.6 μm and a maximum output of 100 W. There is the risk of burns or the like if the laser beam comes into contact with human skin. Therefore, this test was conducted by personnel wearing the firefighting suits and protective eyewear seen in b).
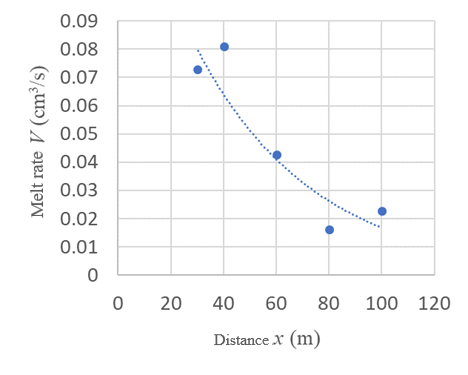
Figure-4 Snow melt rate versus distance
(for a snow with a density of 346 kg/m3 applied to the plywood)
Regression line V =0.16 exp(-0.022x) (V: melt rate, x: distance)
A 5-meter-high temporary structure built at the test field of the CERI (Ishikari City, Hokkaido Prefecture) was used to aim the laser diagonally downward at the snow surface. The melt rate was found to increase with decrease in distance from the laser source. The laser was also found to be able to melt snow 100 m away (Figure-4).
The maximum output of the laser light source used in this study was 100 W. However, it is expected that a light source with a greater output would be able to melt snow accreting to road infrastructure more quickly.
(Contact : Snow and Ice Research Team, CERI)
Research of Technology to Extend the Service Life of Steel Bridges Utilizing Highly Durable Steel
1. Introduction
Corrosion (Photo 1), typical damage of steel bridges, is one of the factors that degrade bridge performance. As a countermeasure against corrosion, members are often coated with paint to prevent salt and other deterioration factors from entering the structure.
Since paint deteriorates over time due to ultraviolet rays and other factors, it must be periodically renewed by repainting. However, the maintenance cost of repainting has become a major issue, and the difficulty of repainting in narrow areas is also an issue.
Thus, we are developing technology to replace the corroded members of steel bridges by utilizing stainless steel, which has high corrosion resistance, even without being coated. This is intended for members that can be replaced independently (secondary members such as sway and lateral bracings) since it is assumed that members will be renewed.
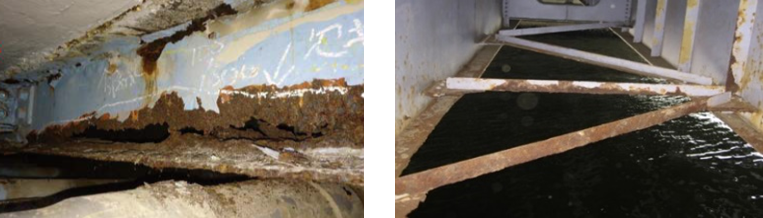
Photo 1 Examples of corrosion on steel bridges
2. Performance verification of stainless steel to be used for steel bridge members
Stainless steel has different properties than the steel materials ordinarily used for steel bridges (hereinafter referred to as “ordinary steel”). It is therefore necessary to understand the performance (load-bearing capacity) of stainless steel when it is used in specific members of steel bridges, such as sway and lateral bracings.
We therefore constructed a test specimen using stainless steel, assuming sway and lateral bracings, and conducted experiments to confirm its load-bearing capacity (Figure 1). As a result, it was confirmed that the load-bearing capacity of the specimens made of stainless steel was equivalent to that of the specimens made of ordinary steel, which had been confirmed in previous experiments.
The experimental results of stainless steel showed a higher load-bearing capacity curve than that of angle and T-shaped cross sections of ordinary steel (dotted line in Figure 2), confirming that the evaluation was on the safe side.
![]() |
![]() between stainless steel and ordinary steel |
3. Countermeasures against corrosion caused by contact between stainless and ordinary steel
Corrosion of metallic materials occurs when different types of metal with different electrical potentials make contact with each other (Photo 2). This is called galvanic corrosion.
As galvanic corrosion also occurs through contact between stainless and ordinary steel, it is necessary to provide insulation between stainless steel as a renewal member and ordinary steel.
We then conducted accelerated corrosion tests under various conditions to verify how to obtain sufficient insulation effects when epoxy resin boards are used as insulators. As a result, it was confirmed that the use of an insulator slightly larger than the contact surface between stainless and ordinary steel, as shown in Figure 3, provides a sufficient insulation effect.
![]() |
![]() that can provide an insulating effect |
4. Application to an actual bridge
After conducting various further verifications, we collaborated with the road administrator and replaced the actual bridge members with stainless steel members on a trial basis (Photo 3). We will continue to evaluate the durability performance in the actual environment by monitoring the condition of the actual bridge with new stainless steel members on a trial basis, and by conducting environmental measurements.
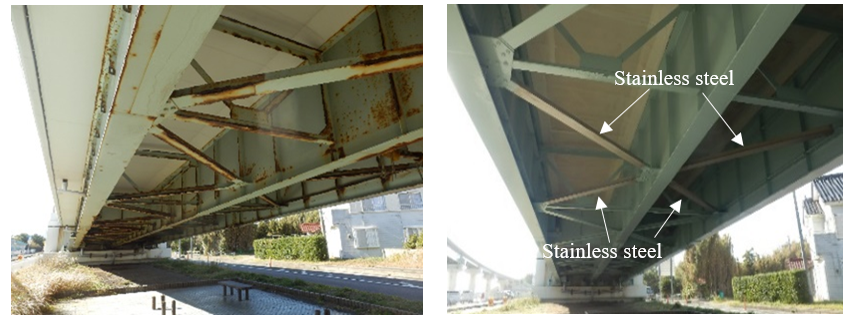
Photo 3 Test application of stainless steel to an actual bridge
(left: before construction, right: after construction)
(Contact : Bridge and Structural Engineering Research Group)